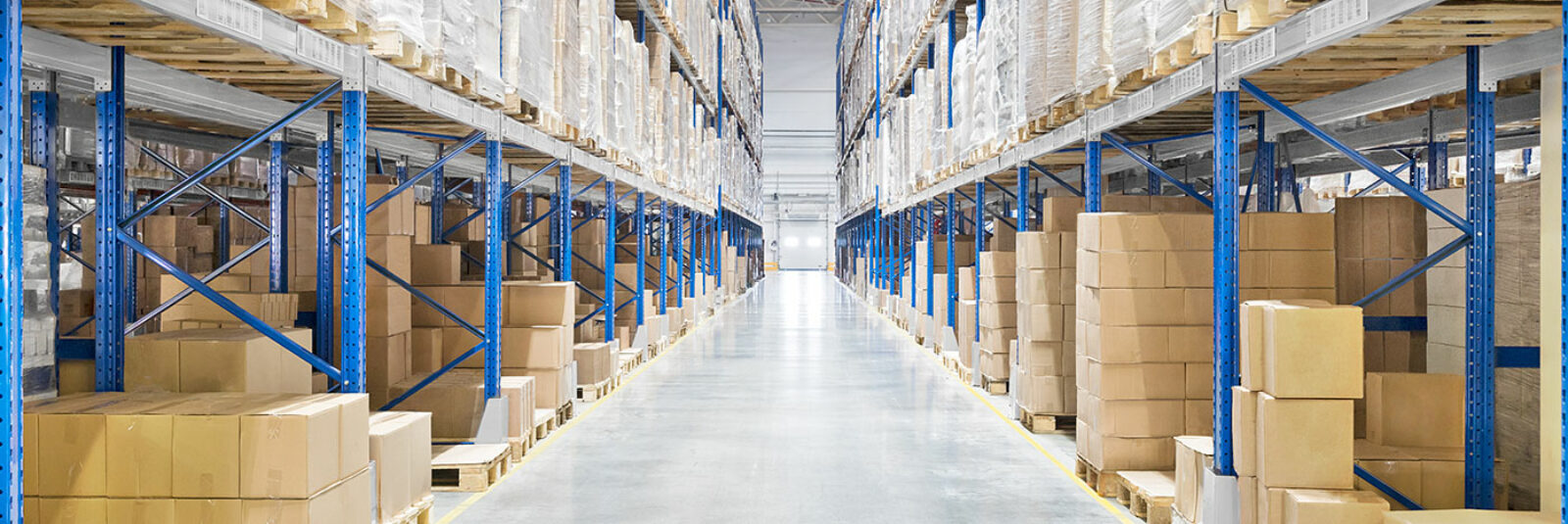
Optimizing the Costs of the Central Supply Chain of a DIY Retailer
Home / Business Cases
Overview
Our client, a DIY retailer, wants to optimize the costs of its central supply chain to offer an optimized service to its network of franchise stores and enable its eCommerce business to bloom.
KEPLER offers the study and costing of different logistics scenarios to determine the target network design that will maximize service, while optimizing full costs.
Context
- Network of 300 stores mainly supplied directly (70%) and with little storage capacity
- Central logistics organized around 2 regional platforms for national ranges and a central platform for overseas imports and promotional batches
- Regional platforms almost saturated (occupancy rate > 95%) with performance levels below the productivity benchmark for the sector (supply cost > 15% COS)
- A strong development challenge for e-commerce amounting to date barely 1% of turnover
Objectives
Category: Improving Responsiveness and Securing Availability
-
Determining the brand’s network design
Cost mapping, used as a baseline for projecting scenarios, allowed us to identify short-term opportunities for cost improvement. We validated a 2-step path, with a first phase of “quick” earnings that did not require any breach in the organization. This allowed our client to build their transition more comfortably, with a better business visibility, compared to CAPEX to be committed.Lysiane Bessonnet, Director
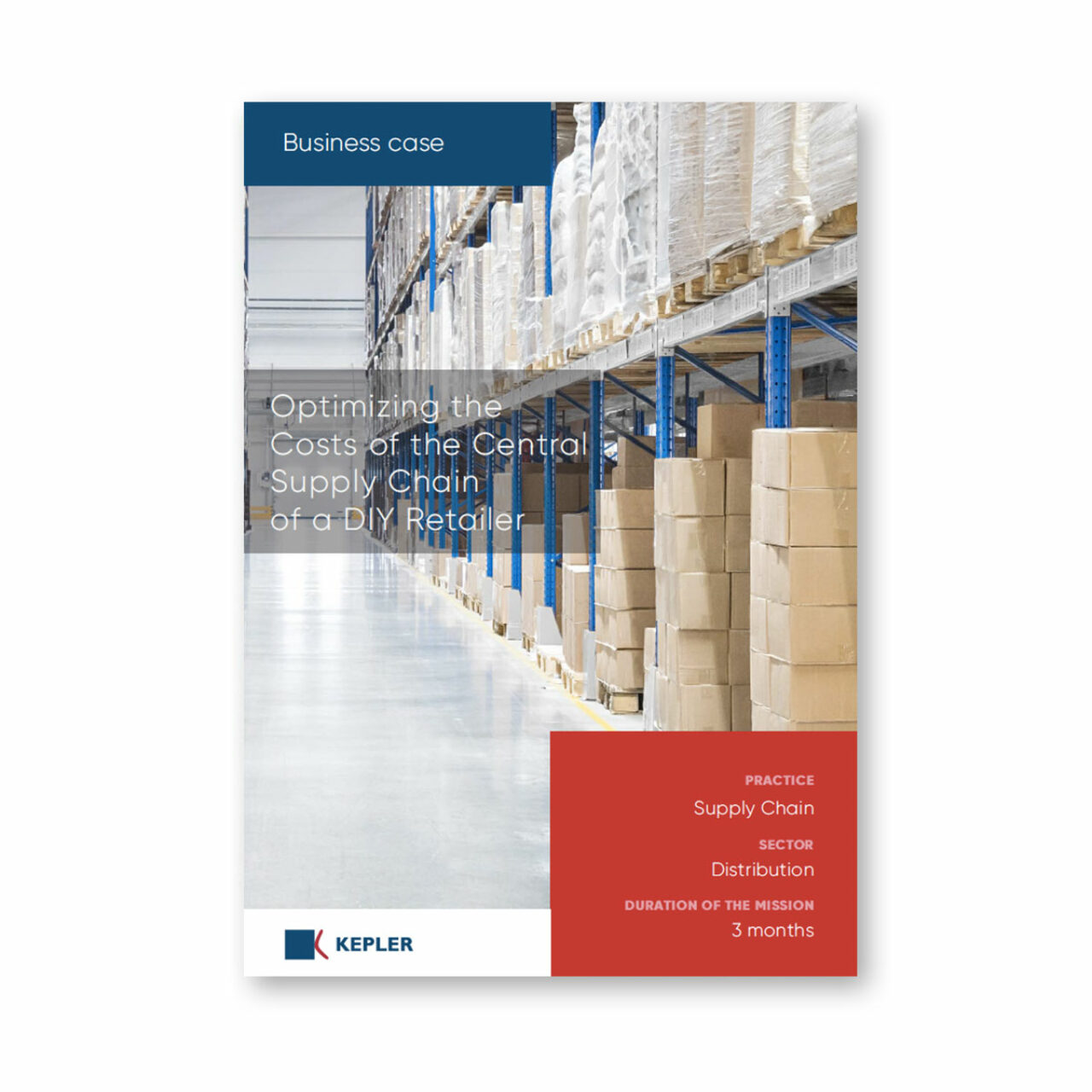
COMPLETE VERSION