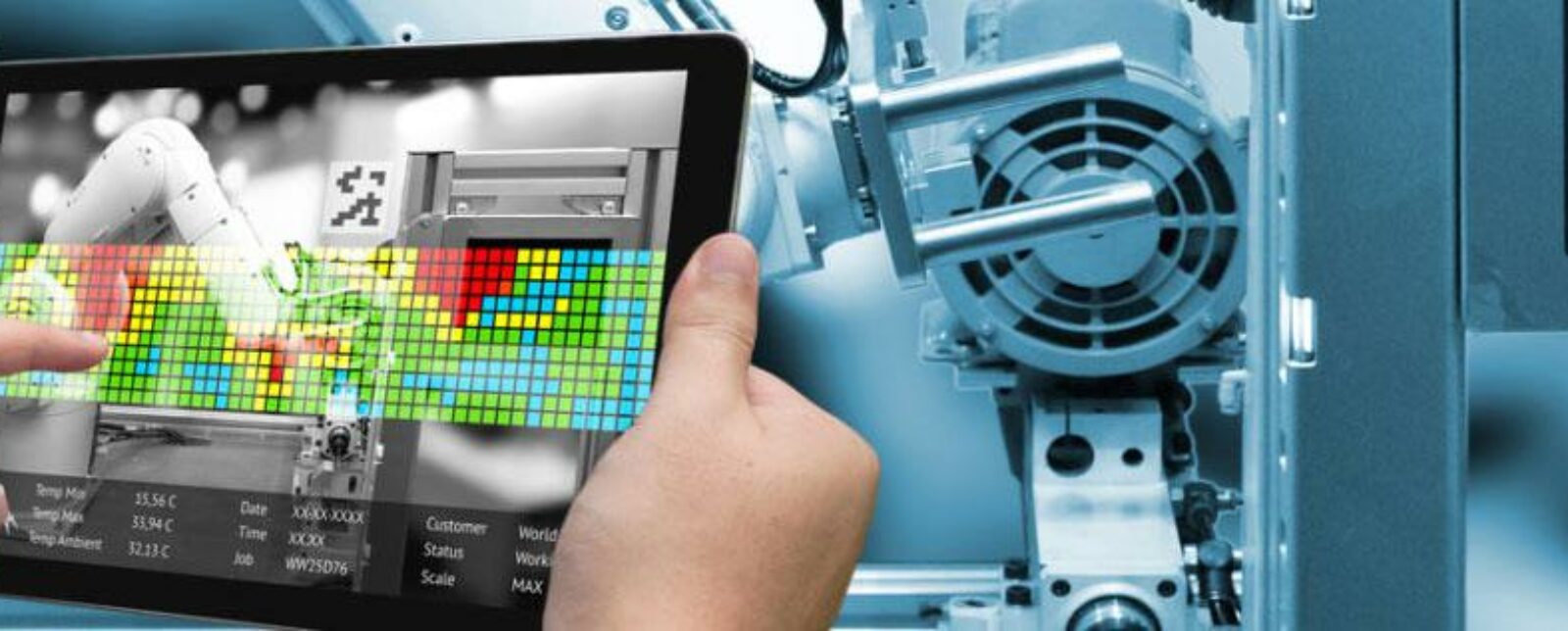
Total Productive Management (TPM) and Industry 4.0 Technologies: State of Play
The Objective of Total Productive Management or TPM
Overall Equipment Efficiency (OEE) classically identifies 16 efficiency losses that it divides into three groups:
- Losses related to equipment,
- Labor losses
- Losses related to materials, tools and energy.
The goal of Total Productive Management is to systematically reduce these losses.
This approach was first set out by the JIPM (Japan Institute for Plant Maintenance) in 1989. It is based on eight pillars,
The Eight Pillars of the TPM Approach - Total Productive Management
Management and Autonomous Maintenance of Equipment
This is the part of maintenance taken over by production operators to make production units more autonomous and flexible. Two types of activity in autonomous maintenance (MA): daily routines (inspection, cleaning, operation control, workstation management (supplies, declarations, etc.)) and contingency treatment (restarts, detection of anomalies , contingency treatment, defined repairs). The deployment of AD involves 7 stages.
Elimination of Waste / Improvements on a Case-by-Case Basis
This covers all waste and causes of loss of efficiency. Finding and eliminating the root cause through improvement activities (Kaizen) must permanently eliminate the dysfunctions.
Control or Maintenance of Quality
The goal is to eliminate the causes of non-quality products in order to achieve zero defects.
Planned Maintenance
This is the part of the maintenance taken care of by the technicians, there are different levels: curative, preventive and predictive. The planning aims to increase MTBF (Mean Time Between Failures), reduce MTTR (Mean Time to Repair), manage spare parts and reduce the proportion of curative interventions.
Improved knowledge and know-How
This involves increasing the skills of production operators as well as technicians.
Safety, Working Conditions and Environment
It is the principle of zero accidents and zero pollution.
Mastery of the Design of Products and Associated Equipment
It is about capitalizing on the mistakes of the past, taking into account all the lessons learned when solving problems, integrating the improvements into the design of the equipment, making them “maintenance-free”, etc.
Efficiency of Related Services or “TPM in Offices”
This involves developing the contributions of support services to TPM activities in production, it is necessary to have consistency in inter and intra service management.
Total Productive Management, Technologies at Work in Industry 4.0
The 8 pillars remain the fundamentals of the industry. But under a large modernization movement called Industry 4.0 and on which we can argue the revolutionary nature, one can ask a simple question: “how is this” revolution “going to consolidate and guarantee ever more efficient maintenance? “.
Bulk data analysis or Big Data, the Internet of Things, artificial intelligence, virtual and augmented reality or even cyber-physical systems appear as a digital upgrade and as many potential levers for improvement.
1 / Big Data Analysis
The term “big data” refers to large, technically complex data sets used in typical data analysis and processing applications. This new approach allows companies to “predict” using in-depth analysis of large data sets that will be actively monitored.
It is estimated that today the amount of information stored is growing four times faster than the global economy. Computing speeds increase in parallel nine times faster. And the advent of the quantum computer promises to further amplify this phenomenon.
From the beginnings of computing until the year 2003, it is estimated that humanity generated 5 exabytes of data. The ecosystem in which we are part of today generates an equivalent mass of data, in just 2 days.
A study of 2,000 companies across 9 major industry sectors and 26 countries shows that 80% of global CEOs recognized the importance of data mining and analytics to their organizations.
The trend today is to extract new data from existing databases. This provides the organization with important technical and business information that enables optimized decision making.
Cloud Computing and Cloud Manufacturing: Operational Counterparts of Big Data Analysis
- Cloud computing is like a scalable platform that helps organizations use IT resources more efficiently, and paves the way for extensive task automation and lower costs generated by isolated systems. Its industrial corollary also called Cloud Manufacturing is the concept that reflects the idea of an intelligent factory, that is, the collaboration of advanced production models with computer technology in the cloud to achieve computerized and focused production. services (Givehchi, Tresk and Jasperneite, 2013).
2 / The Internet of Things (IoT)
The idea of the Internet of Things first appeared in the 1980s, to meet the needs of automated teller machines (Shon, 1996). Many of these devices have since been networked.
This Internet of Things (IoT) is the terminology used to describe physical devices or components that can be connected through the network and have the ability to communicate with each other through RIFD (Radio Frequency Identification) or smart sensors (Gilchrist, 2016b ).
According to ISO / IEC JTC1 (2015) IoT is an infrastructure of interconnected objects, people, systems and information resources as well as intelligent services to enable them to process information from the physical and virtual world and react. However, this is a concept similar to physical cyber systems (CPS).
According to one estimate, around 25 billion devices / objects will be interconnected and will have communication between them, by 2020.
The Internet of Things allows companies to add transparency to processes and make them analytically measurable. These sensors can be worn by operators, placed on production lines, on machines directly or in warehouses.
Likewise, new RFID-type solutions make it possible to guarantee perfect traceability of products along the value chain and also to measure performance on a daily basis thanks to the collection of relevant data. The ability of IoTs to deliver augmented intelligence helps organizations optimize their decision-making ability, ensure efficient data collection, and generate the right reports for their specific environment.
The IoT helps businesses become “smarter” by giving them the ability to analyze their physical processes that were not previously measurable. All of this contributes to better strategic and operational capacity and, in some cases, to a competitive advantage (Kopetz, 2011).
3 / Artificial Intelligence
AI was introduced as a field of research in the late 1950s.
Artificial Intelligence is a sub-field of computing, the sole purpose of which is to give machines or robots such human intelligence that they become independent platforms and capable of making intelligent decisions autonomously (McCarthy, 2007).
There are two types of AI:
- Single-activity artificial intelligence (ANI) which is linked to single-task applications in a very specific field that we are witnessing today (i.e. Go game),
- General artificial intelligence (AGI), a broad, deep concept that includes characteristics surpassing human intelligence in many dimensions such as analytical speed, memory, multitasking, pattern recognition and the ability to adapt with new, self-learned information (Muehlhauser, 2013).
According to Hawking et al. (2014), the success in creating the AGI would be the greatest event in human history, but they are not sure it will not also be the last, unless you learn to curb the risk, d ‘where the hesitant view of experts in relation to AI.
How many jobs will be replaced by robots and AI in the next few years? And how many new trades and positions will be created? The answer is not given, but to illustrate, Japan’s largest bank, Mitsubishi UFJ Finance, recently installed robots for its customer service operations and the IPsoft, a call center, uses a robot from AI “Amelia” capable of self-learning outside of pre-programmed knowledge. “Amelia” can now handle over 60% of all incoming requests.
4 / Virtual and Augmented Reality
The smart factory will be supported by advanced human resource programs in “virtual reality and augmented reality”. Virtual reality (VR) is a computer simulated environment. It is presented to the user as a real environment. It can assist employee training programs and support business processes using compatible digital devices. In contrast, augmented reality (AR) has a head start and allows the user to interfere with a simulated environment (Boud et al., 1999). According to Jason Ganz, CEO of Agora VR “The Internet has allowed us to learn anything – VR and AR will allow us to experience everything”. Experts suggest that some of the management tasks will take place virtually such as strategic meetings and conferences. In addition, VR and AR will help the human resources department with training and the continuous support system for the transition into a digital environment.
5 / Cyber-Physical Systems
In order to make the smart factory operational or functional, we will need “Cyber Physical Systems (CPS)”. CPSs are intelligent systems that bridge the gap between virtual and physical components used in production, logistics and products. This is the concept that combines with the Internet of Services (IoS) to make Industry 3.X possible, which opens up new possibilities for innovative applications and processes. CPS will facilitate the paradigm shift in relation to “business models” and “market models” with all stakeholders in the value chain including suppliers. All these technologies combined with other technologies such as additive manufacturing, for example 3D printing, selective laser sintering, cobotics, AGV, etc., form the basis for the factory of the future, which brings together virtual and physical systems via physical cyber systems. Such a fusion of technical and business processes will provide a gateway to the concept known as “Smart Factory” (MacDougall, 2014).
These technologies exist. The question now is how they contribute to today’s production sites. As part of TPM’s initiatives, the contributions of the digital environment already offer practical solutions that we are implementing with our customers.
Sources :
Boud, A. C., Haniff, D. J., Baber, C., & Steiner, S. J. (1999). Virtual reality and augmented reality as a training tool for assembly tasks. In Information Visualization, 1999. Proceedings. 1999 IEEE International Conference on (pp. 32-36). IEEE.
Gilchrist, A. (2016b). Middleware Industrial Internet of Things Platforms. In Industry 4.0 (pp. 153-160). Apress.
Givehchi, O., Trsek, H., & Jasperneite, J. (2013). Cloud computing for industrial automation systems—A comprehensive overview. In Emerging Technologies & Factory Automation (ETFA), 2013 IEEE 18th Conference on (pp. 1-4). IEEE.
Hawking, S., Russell, S., Tegmark, M., & Wilczek, F. (2014). Stephen Hawking: \’Transcendence looks at the implications of artificial intelligence-but are we taking AI seriously enough?’. The Independent, 2014(05-01), 9313474
Kopetz, H. (2011). Internet of things. In Real-time systems (pp. 307-323). Springer US.
Shon, S. W. (1996). U.S. Patent No. 5,499,238. Washington, DC: U.S. Patent and Trademark Office.
MacDougall, W. (2014). Industrie 4.0: Smart manufacturing for the future. Germany Trade & Invest.
McCarthy, J. (2007). WHAT IS ARTIFICIAL INTELLIGENCE? Retrieved March 15, 2017, from http://www-formal.stanford.edu/jmc/whatisai/
Muehlhauser, L. (2013, September 15). What is AGI? Retrieved March 26, 2018, from https://intelligence.org/2013/08/11/what-is-agi/