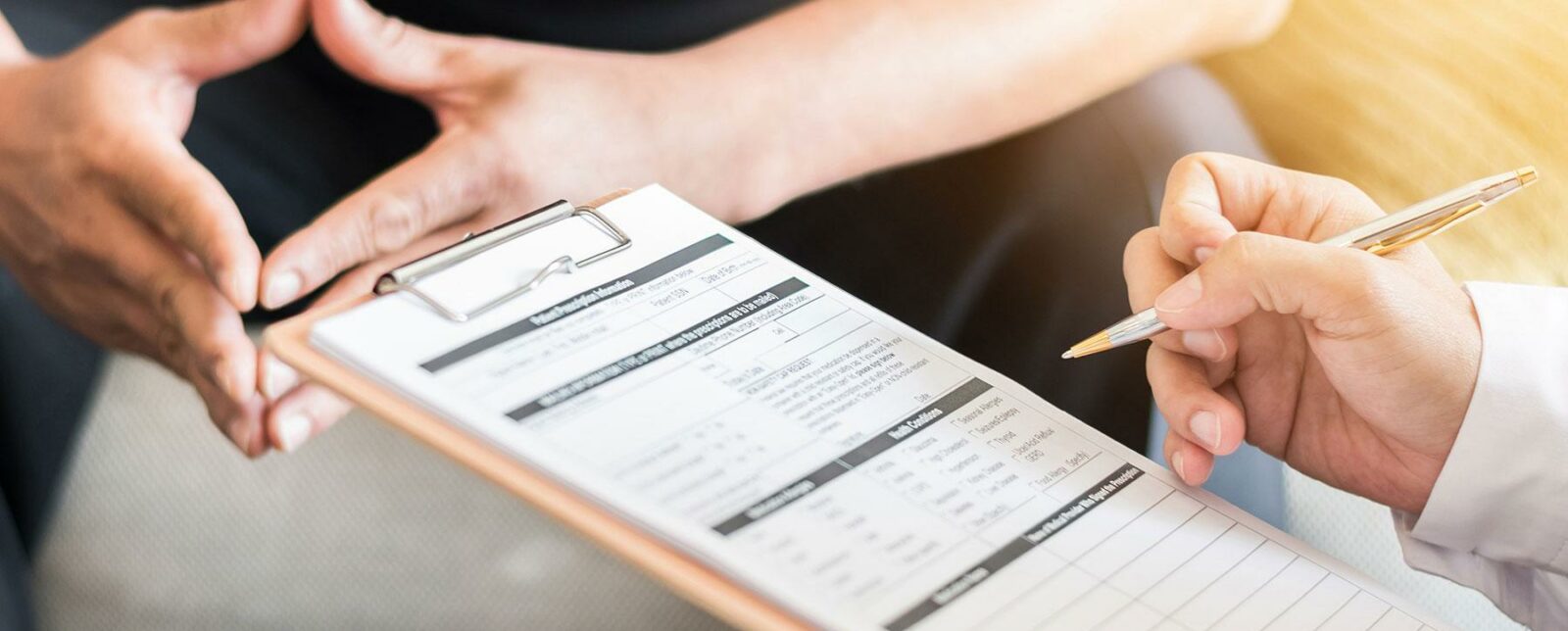
Flash Operations Diagnosis or How to Build a Transformation Roadmap
Reminder of the Major Business Challenges
The Major Issues Affecting Operations Today Can be Summarized As Follows:
- Customer satisfaction
- Improved EBITDA and cash flow
- Competitiveness
- Differentiation
- Innovation
- Quality
- Internal or external growth,
- Mobilization of the team.
The Main Areas for Improvement to Meet These Challenges
Service Rate
Improve customer satisfaction (quality, time, PIC / PDP process, flow and stock management, capacity management and industrial flexibility …)
Quality
Reduce product non-quality – root cause analysis, predictive analysis – and supplier – specification definition, audit and monitoring, supplier development.
Industrial Cost Price
Strengthen competitiveness – maintenance improvement plan, CAPEX, purchasing, lean manufacturing, digital … – and generate cost savings by reconciling finance, production and trade.
Industrialization
Streamline and make more robust the process of introducing new products, in particular using multi-business Value Stream Mapping (VSM).
Project / Program
Control projects: meeting milestones, reducing time without added value, improving validation processes and time-to-market, defining the product as needed, designing at target cost.
Among the Responses Offered by KEPLER to These Different Challenges: Flash Operations Diagnosis
KEPLER, with its many operational experiences in the industry, from innovation, to purchasing, through the supply chain and operations, provides concrete, practical, accessible, robust and pragmatic solutions around best practices tested and its benchmarks.
An Ecosystem of Digital Partners
KEPLER relies on its ecosystem of partners and digital solutions to help its customers build a precise roadmap with simple Proof of Concept (POC) to validate these new solutions.
Among the subjects addressed:
- Artificial intelligence
- Connected objects
- Real time monitoring
- Machine learning
- Predictive analytics
- Dematerialization
Methodology for a Flash Diagnosis
Step 1: Understand the Challenges of Each Company, Listen to the Teams and Collect Their Expectations
- Objectively analyze the current situation in terms of operational performance, financial results, interfaces between different business sectors, management priorities and build an ambitious goal with management and operational staff
- Identify areas for improvement, current actions and propose innovative levers complementary to initiatives already implemented (tools / methods / digital, management system, management) to achieve the objective
- Giving teams a (logical) perspective and understanding the root causes of non-performance
Step 2: Perform a Rapid, Participatory Field Diagnosis in 4 Weeks Maximum, Sometimes Shorter in the Case of Operational Due Diligence.
- Identify areas for improvement (industrial organization, supply chain, throughput …)
- Build an operational, ambitious and pragmatic program
- Mobilize and align teams on the target and the associated action plan
The deliverables of a Flash Operations Diagnostic
The 4 Components of the Finalized Flash Operations Diagnosis
Costing of the economic issues of the Business Plan (EBITDA, WCR, CAPEX) and human (change management plan).
A transformation plan including:
- Phasing,
- Methods,
- Digital solutions,
- Project organization,
- Deliverables by initiatives,
- Performance measurement.
Plan synergies within the framework of accumulation.
An assessment of the risks and key success factors for the deployment phase.
Expected Results of a Flash Operations Diagnostic
During the deployment plan, our operational support allows teams to increase their skills in order to fully take on new practices.
Continuous improvement and the fight against waste become natural processes.
- Multi-company interfaces are becoming more fluid.
- In the case of accumulations, integration is faster and more efficient.
In the end, the goals are met … and even exceeded!
Infographics
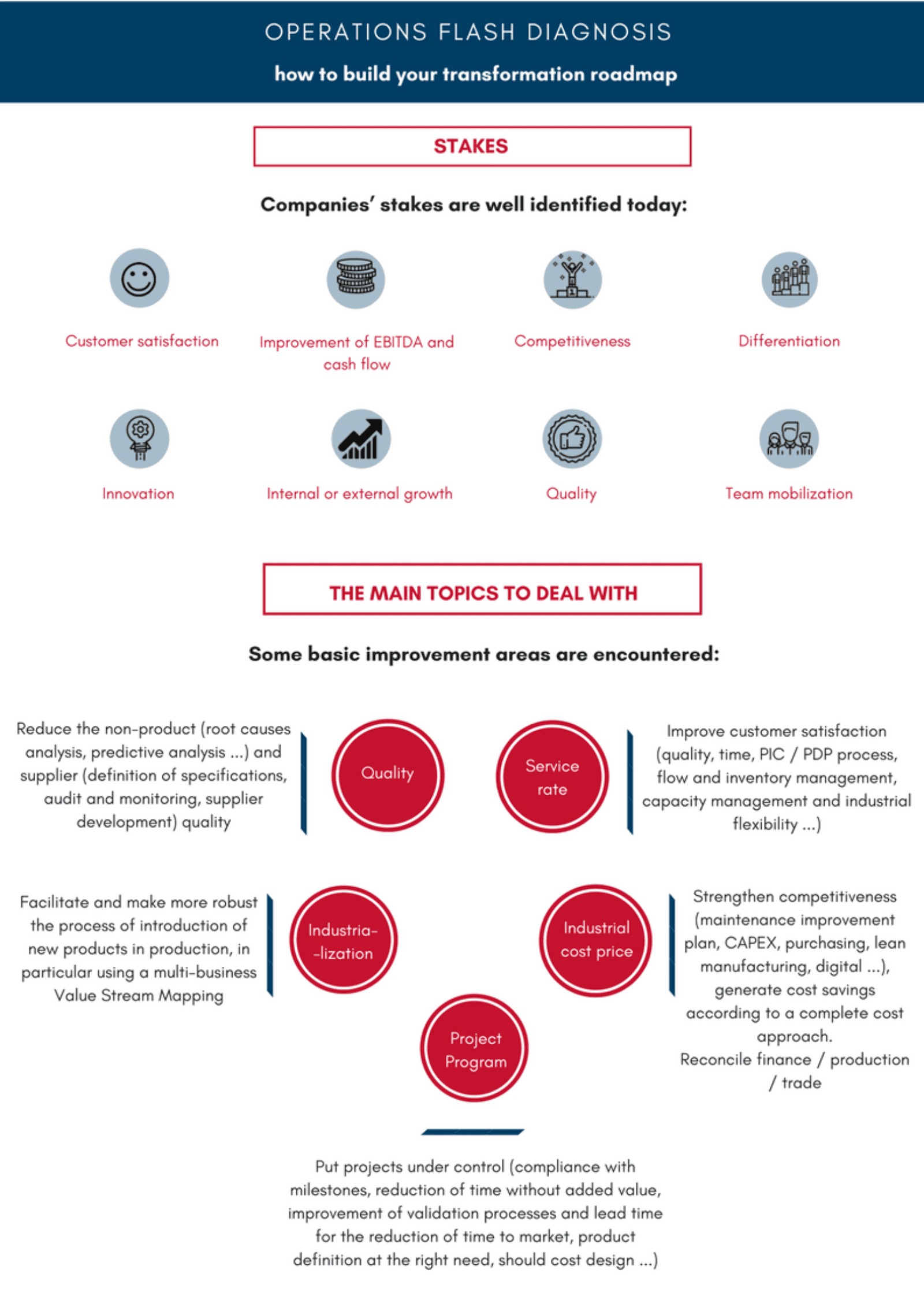
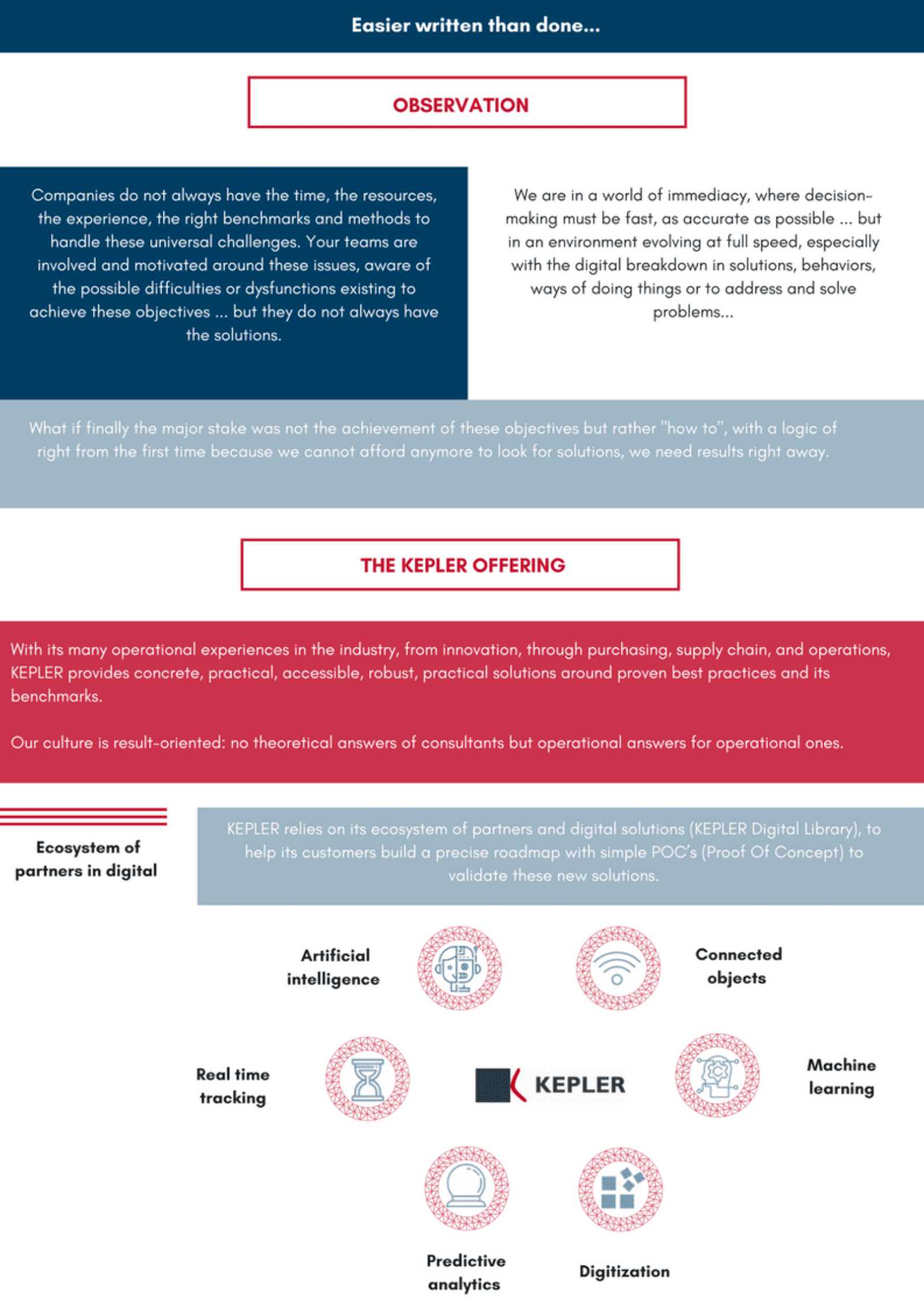
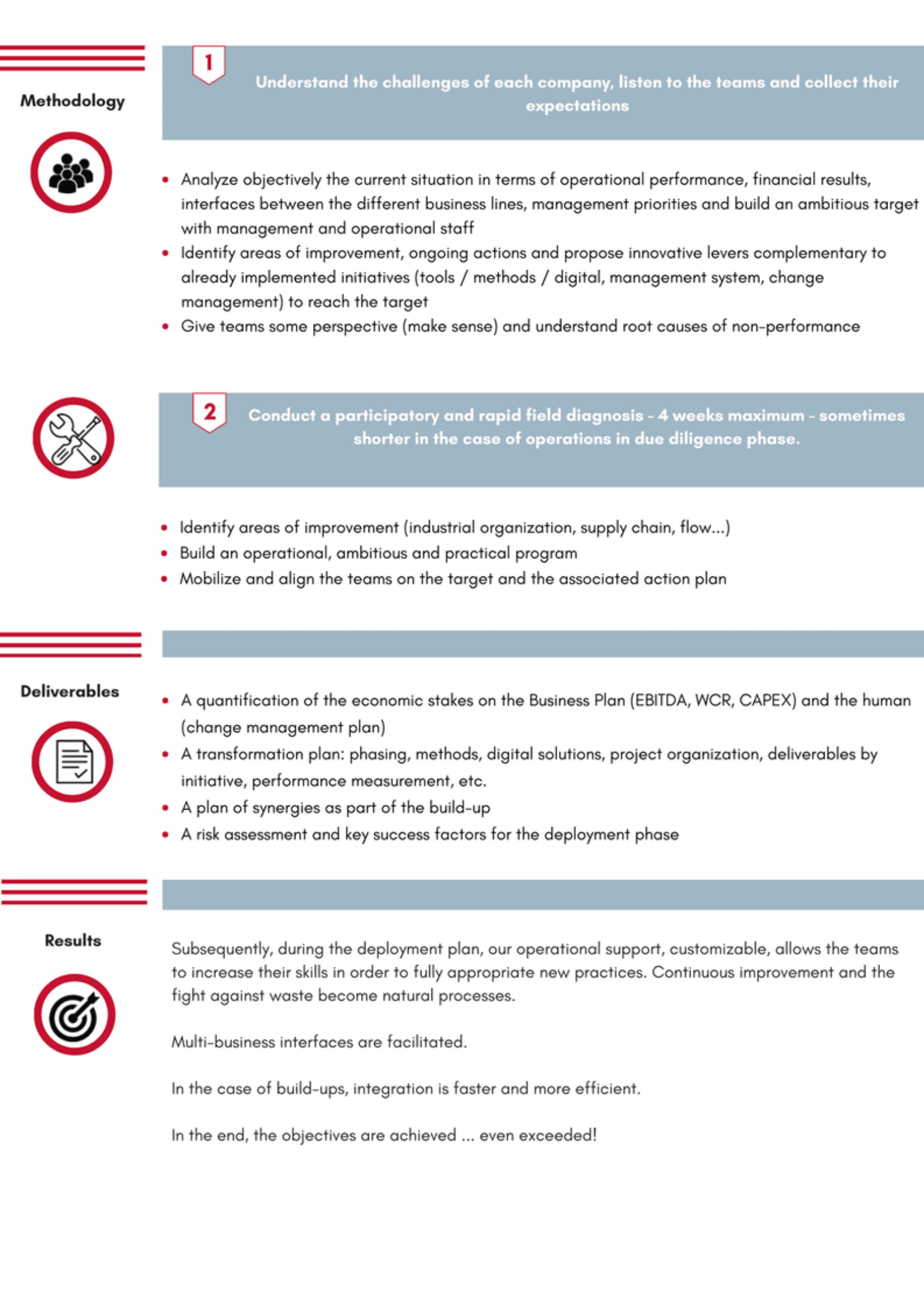